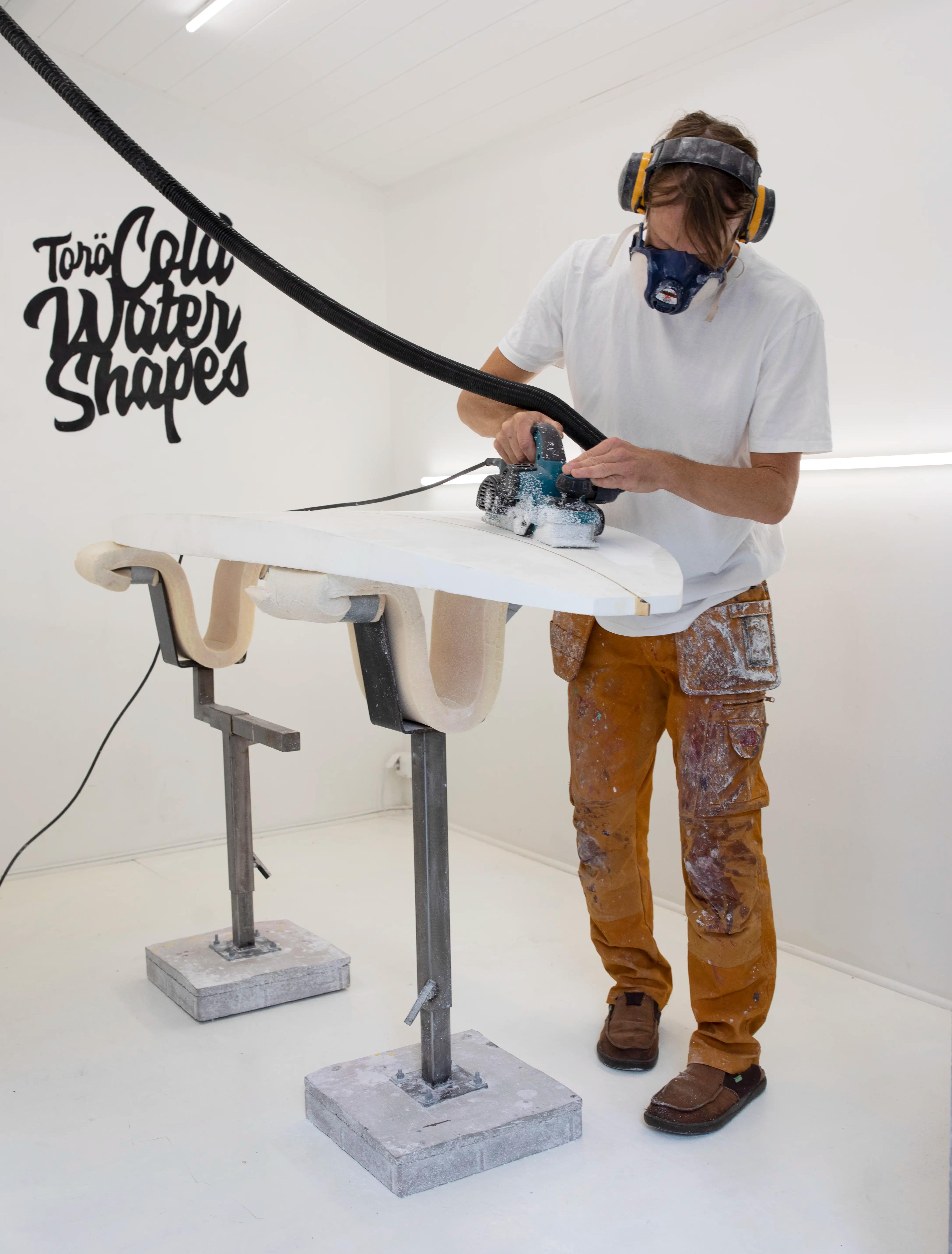
FEBRUARY 2022
Surfboard shaper with his own shack a stone's throw from Sweden's surf mecca on Torö Stenstrand
Words by Pelle Jansson
Photography by Jens Andersson
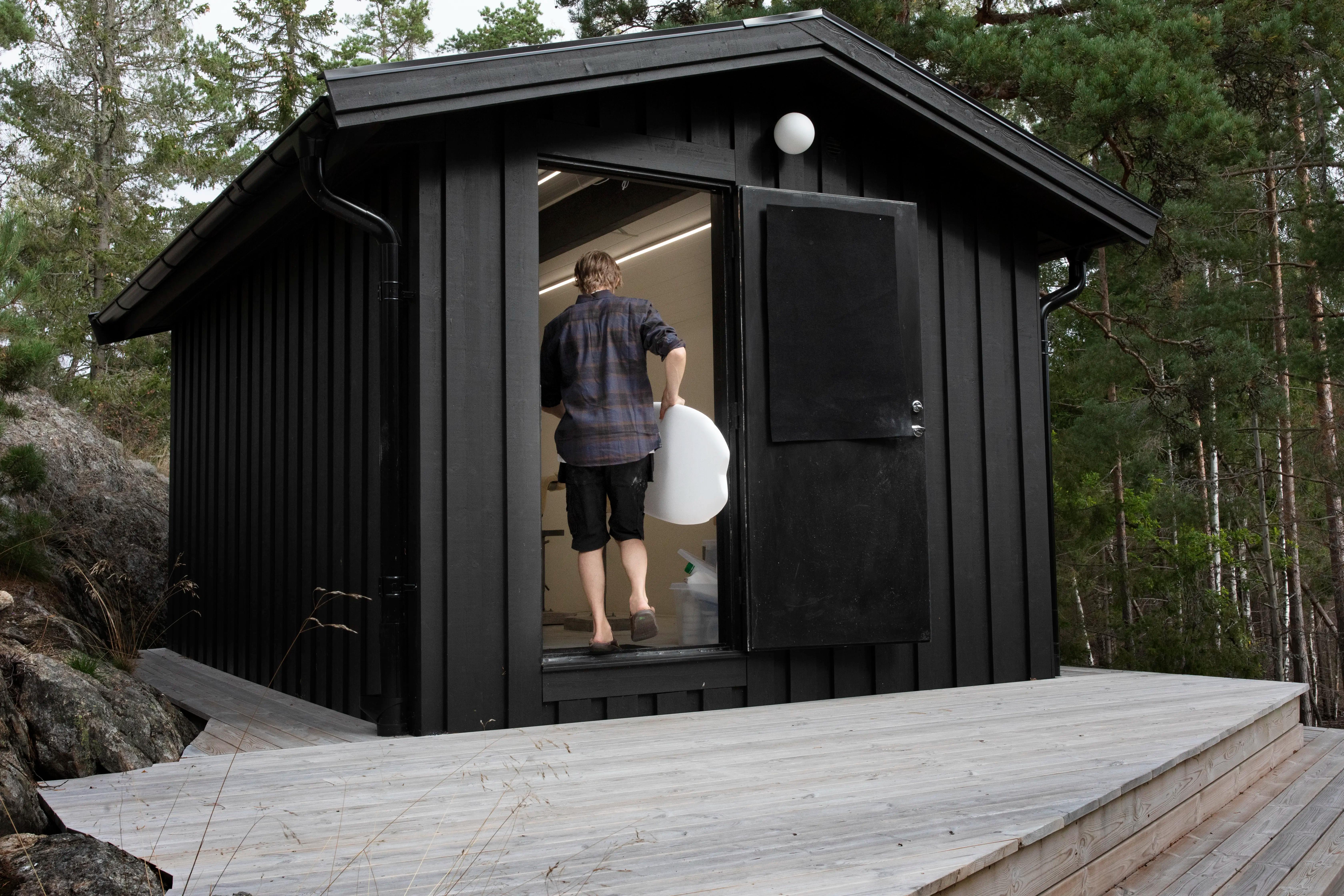
In the middle of Torö, a mythical island and the southernmost outpost of the Stockholm Archipelago, you’ll find a dark-painted shop that blends well into the surrounding nature of pines and granite cliffs. Through the shop's only window, you’ll see a large black logo on a white wall that says "Torö Cold Water Shapes".
This is where Matte Wiberg spends much of his spare time. Sweden's most famous surfing spot, Torö Stenstrand, is just a couple of kilometers away, so by Swedish surfing standards, Matte has his workshop right in the middle of the Swedish surfing paradise.“I built my boards during evenings and weekends and it was a perfect solution at the time. You actually don’t need so much space, the most important thing is that you have a well-functioning method for dust extraction. It still gets messy anyway, so it was not an option in the long run”.
- When we bought this summer house, I realised that this was where I wanted my own private workshop to be. It would be available day and night - all year round. It took me a few years to get round to building the shed. But when it was ready, it was just a matter of moving in - I already had all the tools.
Matte is a co-founder of the design agency “Visual ID” which he runs together with two colleagues who are also surfers. Their common interest gave Matte the freedom a while ago to create a glass corner in the office on Södermalm in Stockholm, put a Festool vacuum cleaner in it, and installed a fan system.
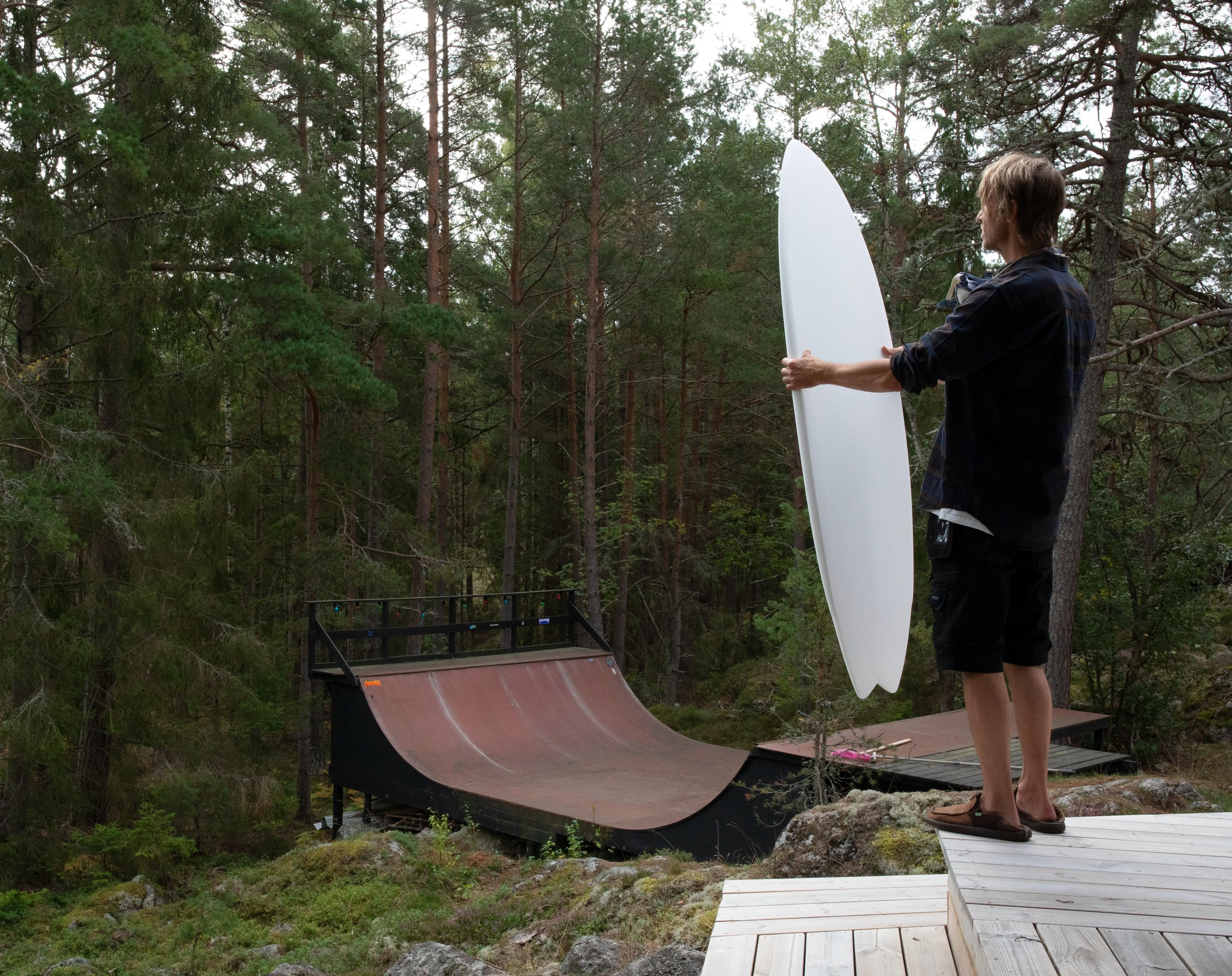
It’s obvious that Matte has a passionate sense of colour, shape and finish – and this is something that was noticeable already when he was a young teenager.
Matte has an active background in every board sport you can think of and built his first snowboards and windsurfing boards already in the 80s. He became a promising snowboarder and could easily have pursued an international career in the sport, so it came as a huge surprise to most of his friends when he actually resisted the urge to become a full-time professional snowboarder and instead invested in studies and a career as a designer.
In 1991, Matte started at Konstfack where he studied industrial design and graphic design for five years. Even at Konstfack, Matte's curiosity and attraction to breaking new ground was noticeable. As his final project, he chose to build a digital didgeridoo in carbon fibre.
- Yeah, it was a really fun project. Getting to know this instrument first, talking to musicians and getting to understand how the instrument actually works, figuring out both interior and exterior design and actually building it with the most advanced materials and techniques of the time was incredibly fun and educational.
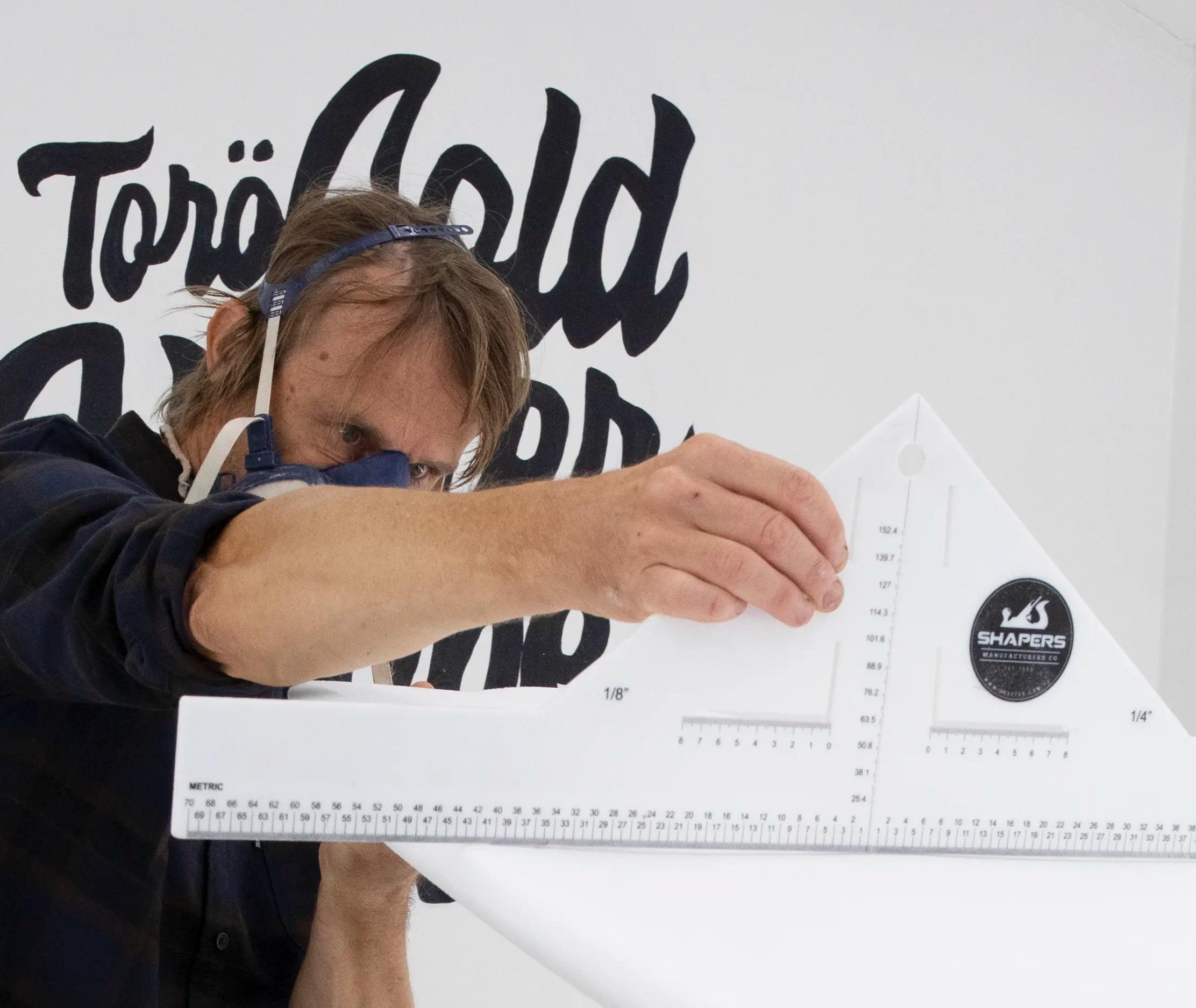
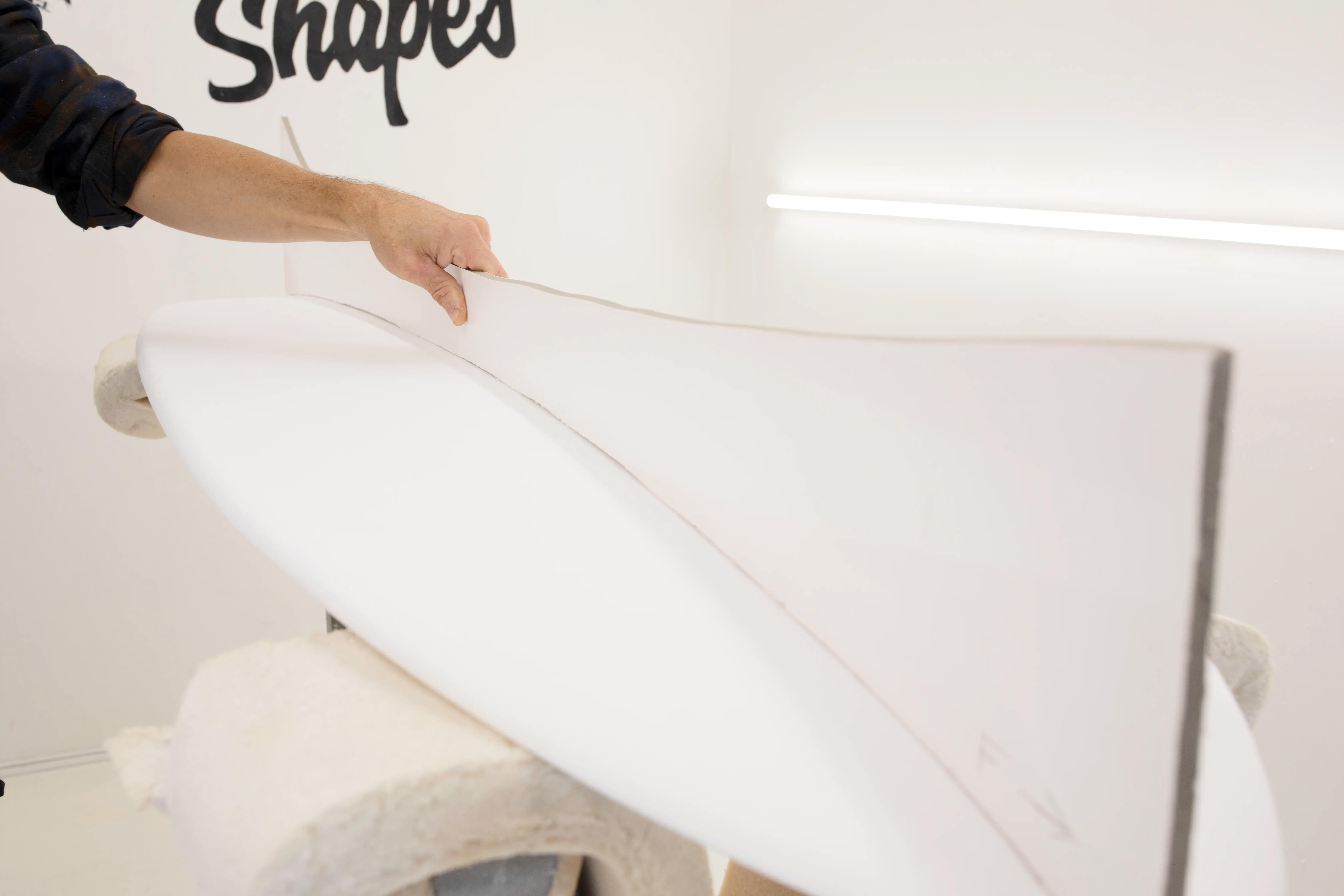
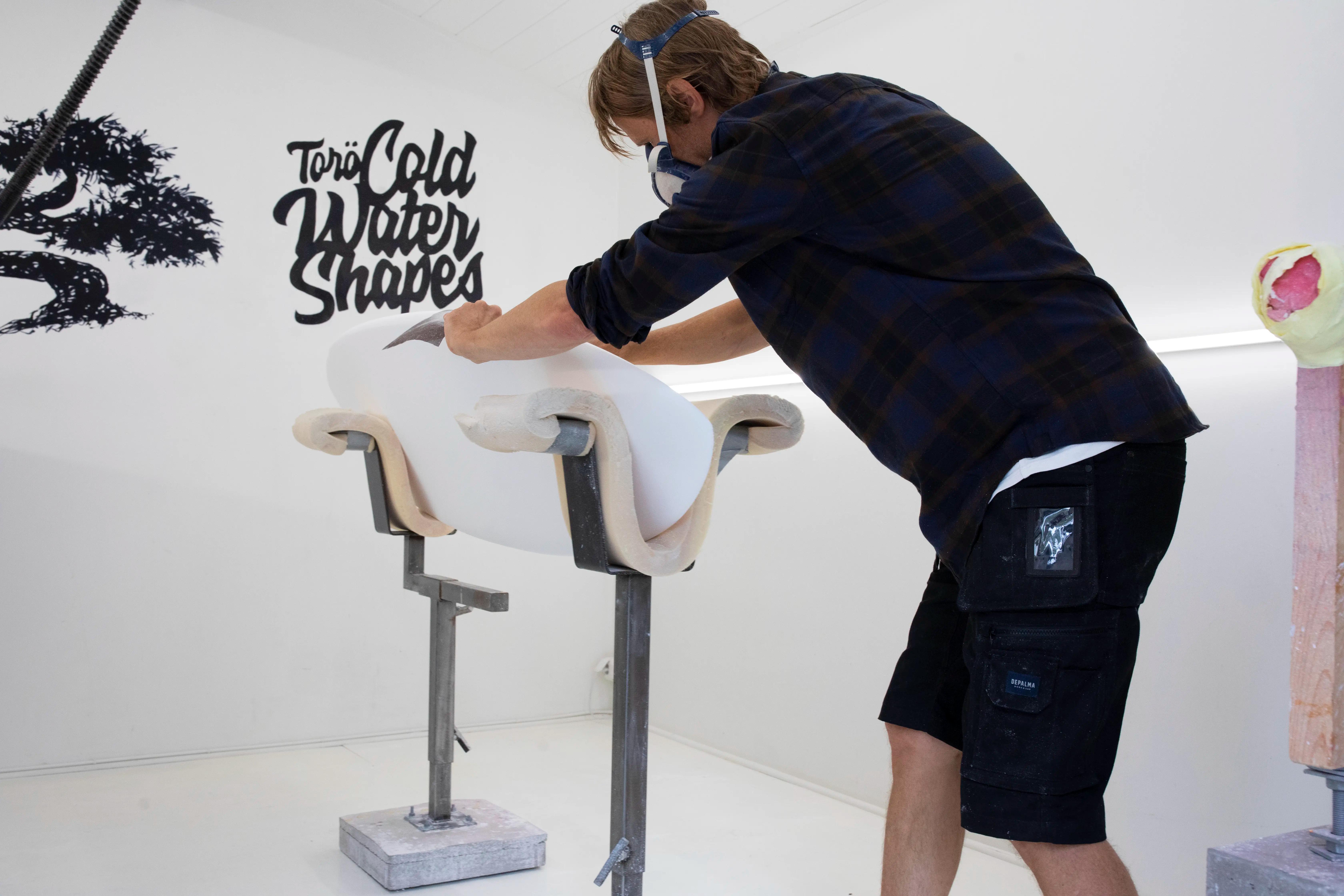
One of the challenges with building surfboards is that the process consists of so many steps and also different types of work, so it's really a job for three or four people. The shaping itself is just a small part of the whole process.
Shaping is about the sculptural moulding work where you are processing a very fragile foam material. You have to be careful yet committed to get the shape just right. This part is very meditative and addictive.
The colouring process involves masking up, mixing colors and spraying directly onto the foam.Alternatively, pigments can be used in the plastic when laminating.
Lamination, or "glazing" involves laying layers of fiberglass together with hardening plastic. This is actually the most difficult moment with the greatest risk that something could go wrong. This is followed by the unglamorous job of grinding, which is done in several steps, and polishing. In between, finboxes and leash plugs are also milled in.
When you’re done with a board, you start again from the beginning with an unshaped block of eps-foam and a bunch of new ideas. You’ve already forgotten the last moments from the previous project which were quite monotonous and demanding.
There’s never an option to go back a step and rework when building surfboards.

"There’s no Ctrl Z button to press, as there is in the digital world. This means that every step in the process must be done methodically and accurately. I make careful preparations and check very often with my templates so that I know I’m on the right course. I haven’t yet built so many boards that I just “freestyle”. I like accuracy."
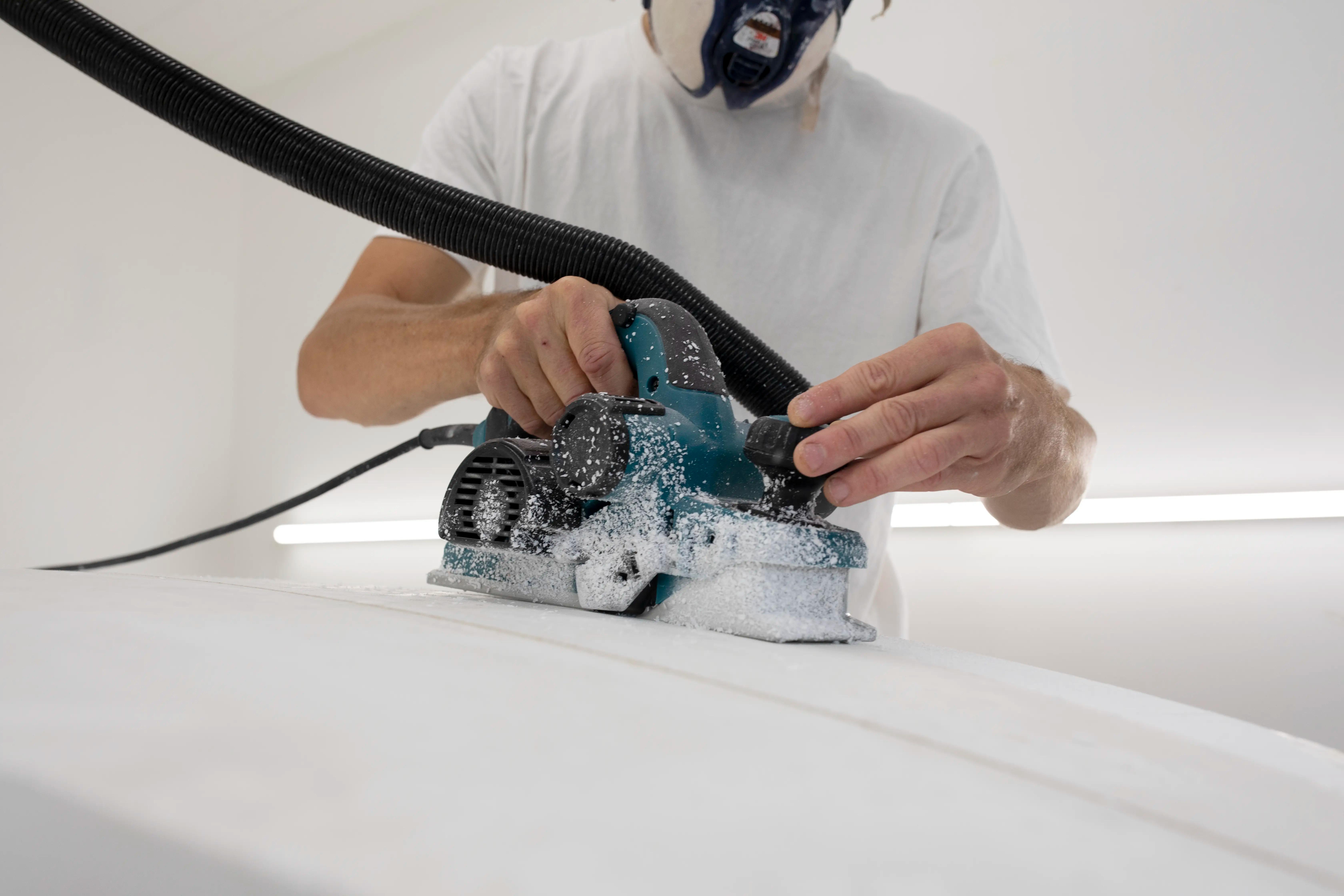
The tools Mattias use to shape the board include an electric planer from Makita. He has replaced the planer steel with a spiral cutter that was ordered from the USA. It makes planing smoother and eliminates the risk of chipping. He also use a classic surform rasp for some hand-chasing.
- The closer to the finished shape I get, the more sanding blocks and sandpaper I need to use. I also have grinding nets in different sizes. The net lets through the material that is ground away and you can form rails in a good way. I also have a set of profiled sanding blocks that are used for the various concavities, among other things.
Mattias has placed fluorescent lamps horizontally on the walls in the workshop, at working height. It provides a trailing light so that he can easily see irregularities and defects in the surfaces he processes.
- The reward of painstaking accuracy comes when you’re done with the shape - then you know that the core is as perfect as it can be before it’s time for painting and lamination.
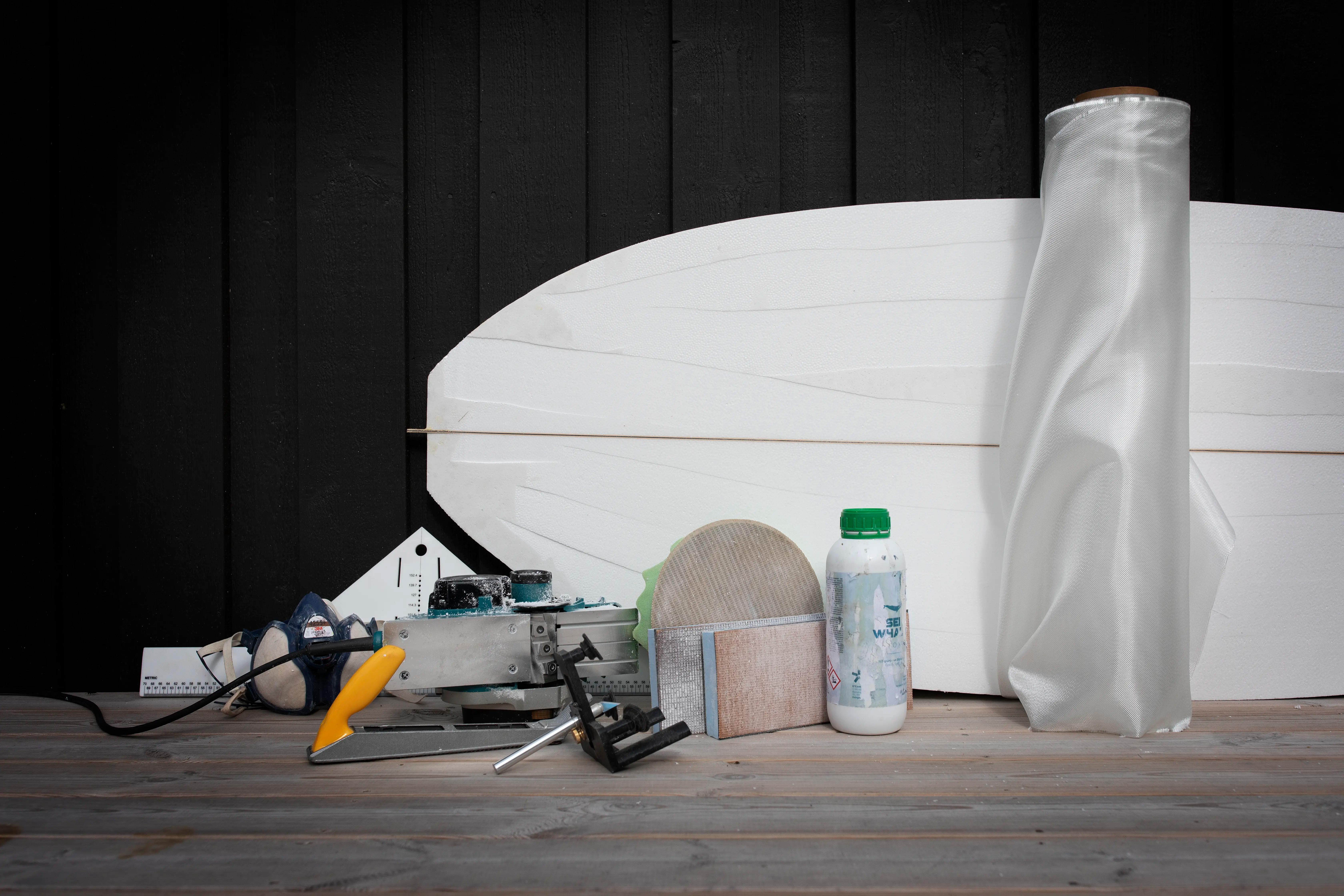
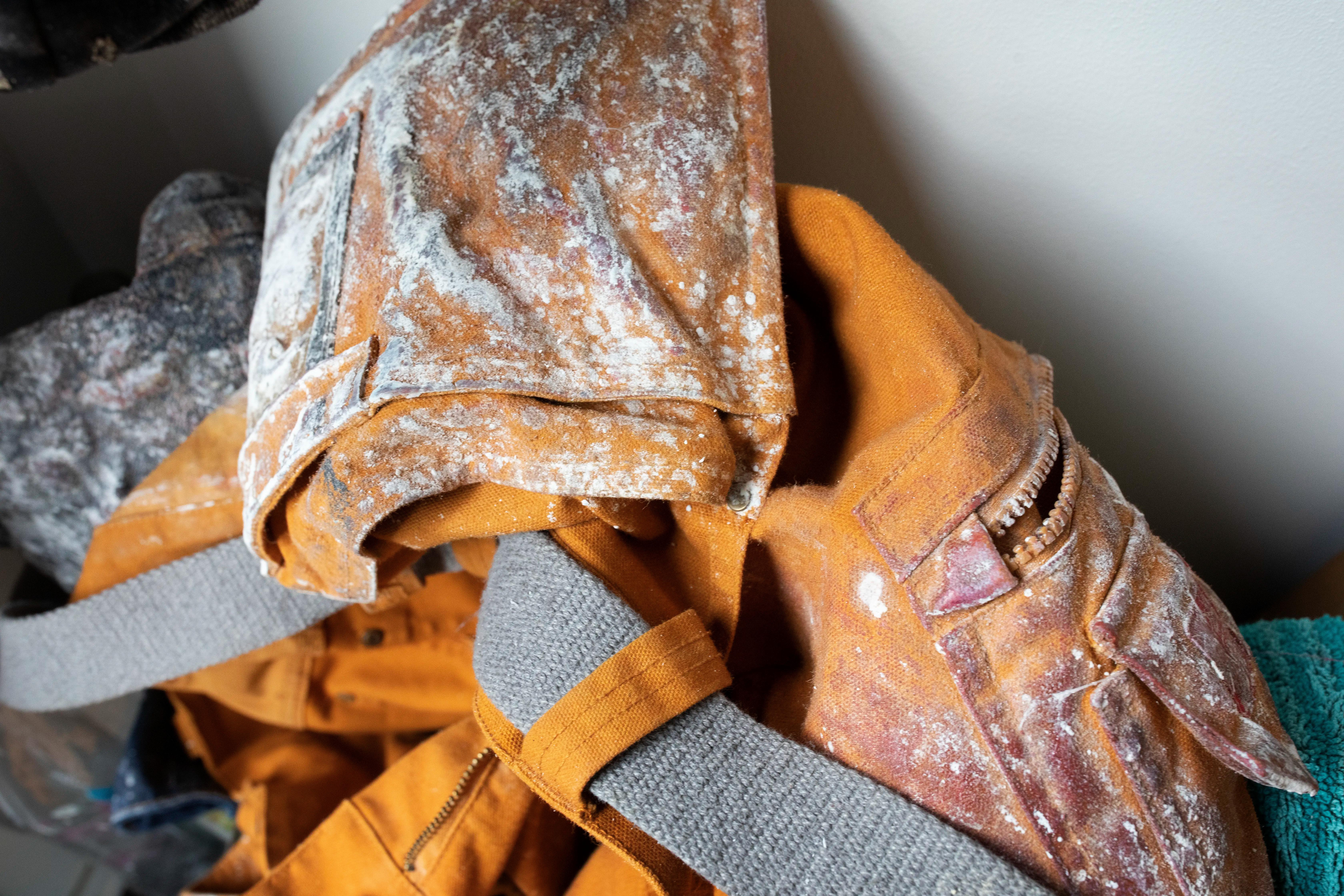
When you build surfboards, you have to consider environmental and health aspects. The most commonly used materials in board construction are polyester and PU foam. But the process commonly uses acetone as a solvent which is strong-smelling. An alternative construction is epoxy and EPS foam which is considered more environmentally friendly and usually results in more durable boards. Nowadays I only build boards with these materials as they are bio-based and result in ecologically more sustainable products, while avoiding unhealthy solvents and odors. Compared with polyester, using epoxy means a slower process, more finishing problems and greater cost, but it is worth it. Regardless of the choice of material, there is a lot of dust when you process the foam, airbrush or grind the laminate.
- There’s a hell of a lot of dust on all sides and edges, but I have good ventilation and good dust extraction and of course I work with a mask with a dust filter and gas filter.

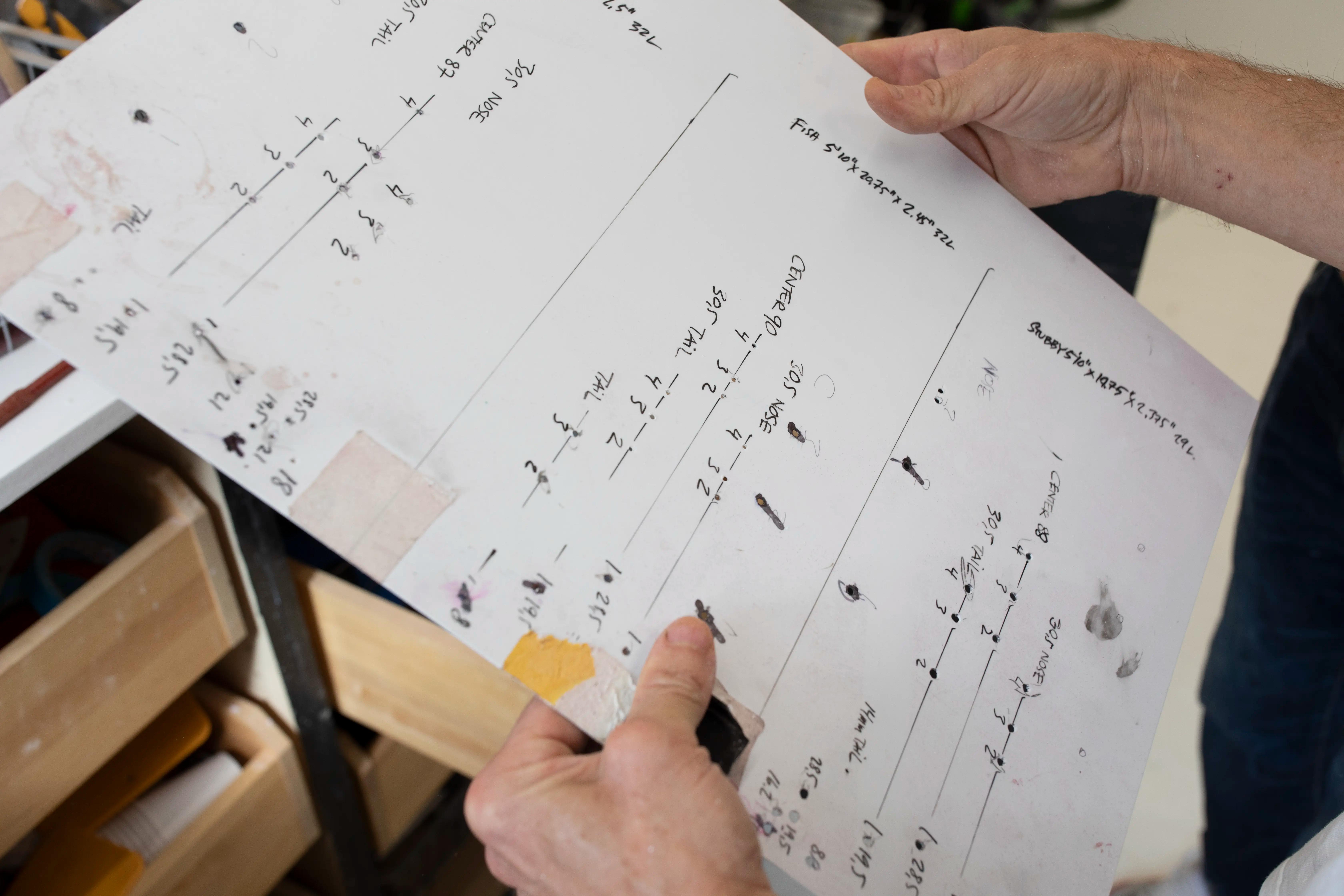
It takes about a week of productive work to build a board. Curing and drying are the most time-intensive processes. Once the board is ready, the standing surface is waxed on the top, so that the surfer gets a better grip. The original wax is called "Dr Zog's Sex Wax" and is intimately associated with surf culture. Of course there are a lot of different types, much like with ski wax for cross-country skiing.
- Yeah, the wax comes in different degrees of hardness for different water temperatures. From cold water to cool water and tropical water. Then you have different smells and colors to choose from.
When you look beyond the prevailing image of surfing as simply "It's you, the board and the ocean”, there are a thousand aspects of surfing that the surfer needs know about and learn to adapt to. When interest turns to passion, the thirst for knowledge and perfection can be limitless. Just mention "rocker line", "quads" or "channels" to the initiated surfer and he or she will likely launch into an animated monologue.

Profession
Industrial designer, graphic designer, board builder
Passion
The family of course. But otherwise, surfing, skateboarding, snowboarding, construction projects with tool mixing, music (drummer in the band "Strindberg Som Tortyr") and building surfboards are at the top of the list.
Geeky facts
If you’re doing special things and cultivating a nerdy interest, it’s inevitable that you’ll also become a “materials nerd”. Matte is no exception. He knows what he wants and, with the help of Google, knows where he can find it and therefore he orders special materials, tools and components from all corners of the earth.
“The blanks (foam core) usually come from the USA and Australia, but I usually use locally-produced EPS. Australia, where surfing is a gigantic movement and the range of building materials and accessories is large, has the most choice. Bio-based organic epoxy is available in Europe and here you will also find a large selection of fiberglass”.
He ordered the spiral cutter for his electric planer, which is the tool he uses the most, from a store in the USA.
Mattias's Outfit

Craftsmen Stories
David Sundberg - Guitar builder
DePalma visited David Sundberg in his tiny workshop out amongst the fields in the middle of the very picturesque Swedish countryside.
The place is a craftsman’s dream in miniature and its reputation for building guitars with unique sounds is way bigger than the workshop itself.