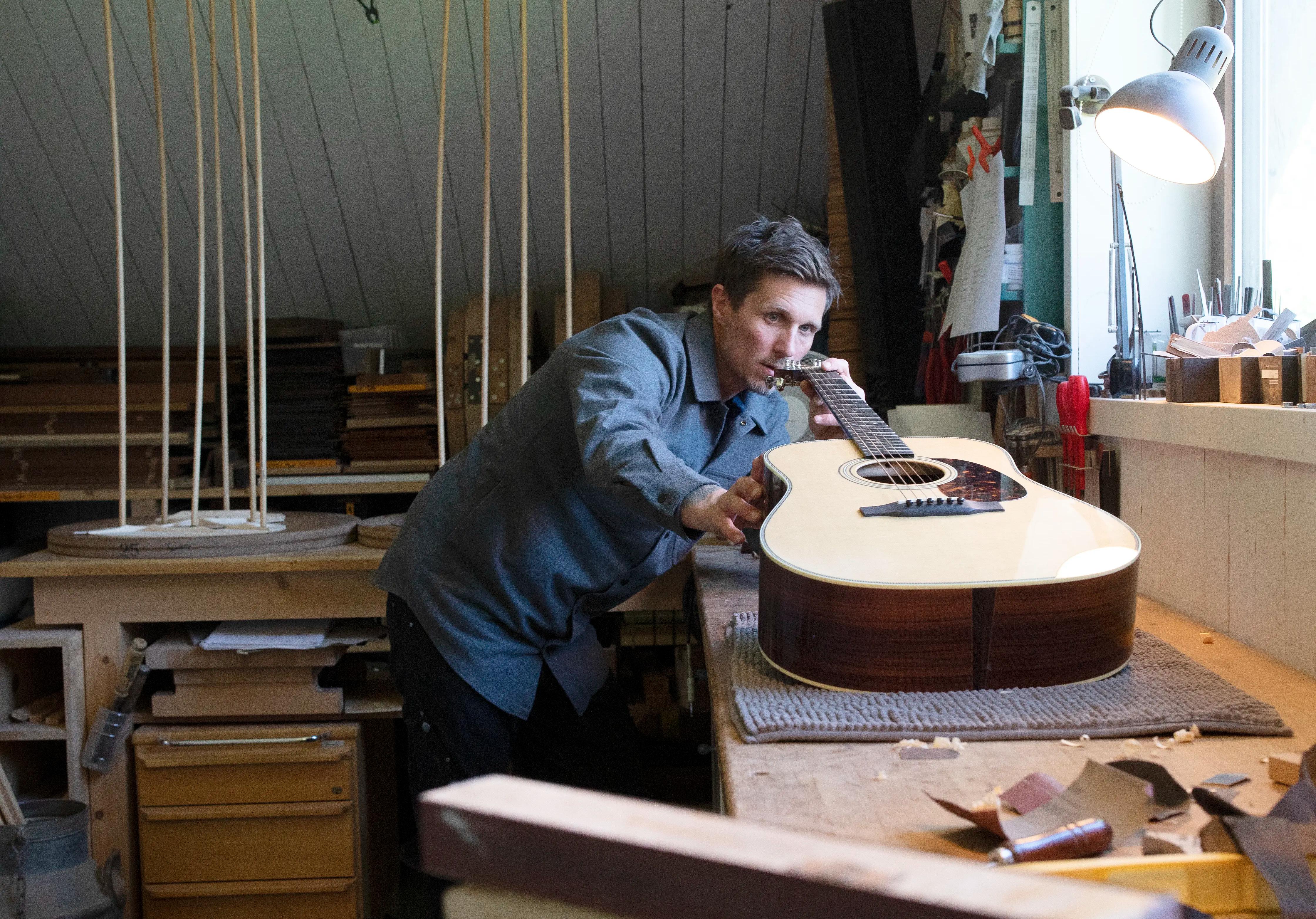
FEBRUARY 2022
DePalma visited David Sundberg in his tiny workshop out amongst the fields in the middle of the very picturesque Swedish countryside. The place is a craftsman’s dream in miniature and its reputation for building guitars with unique sounds is way bigger than the workshop itself.
Words by Pelle Jansson
Photography by Jens Andersson
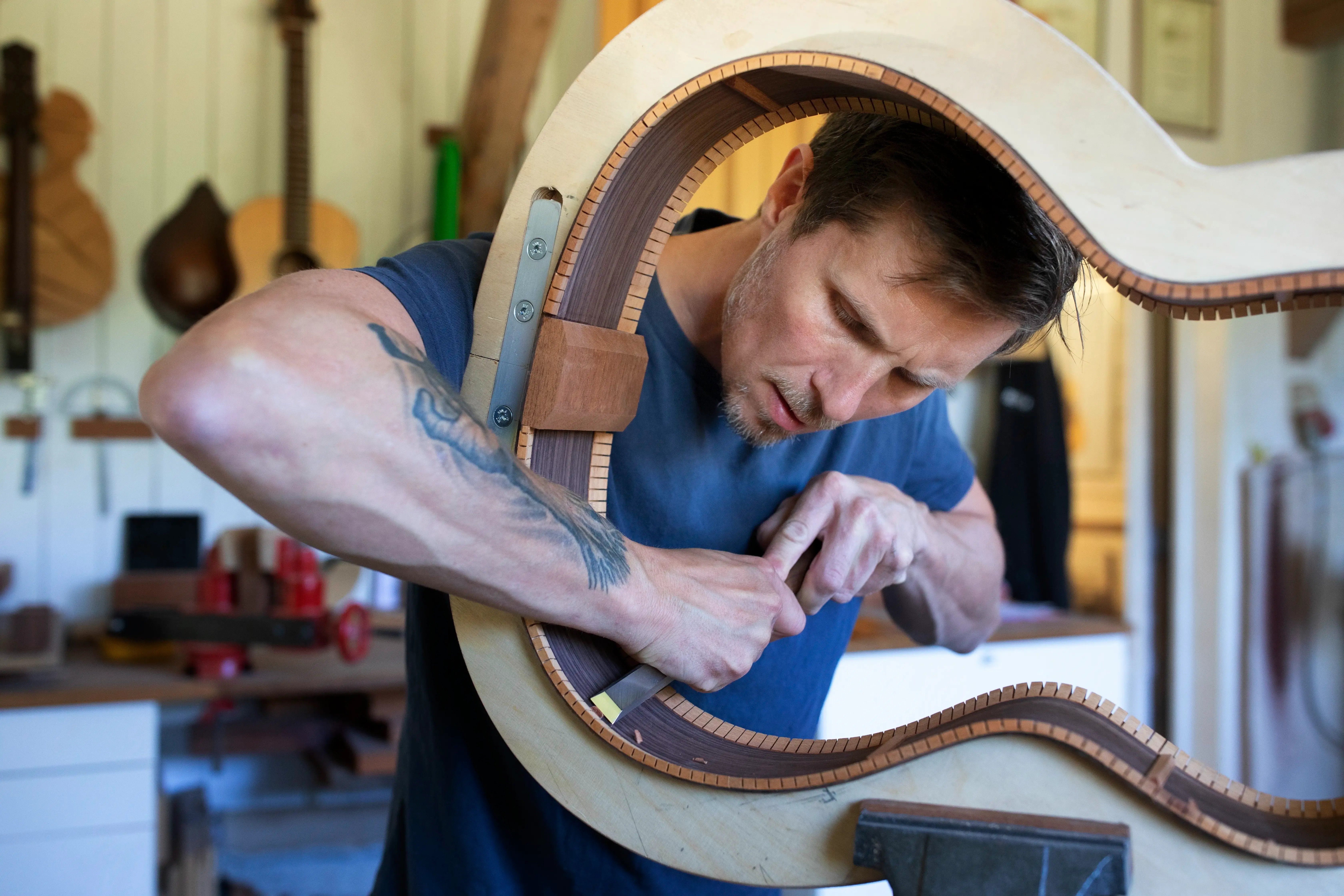
David Sundberg is a guitar builder by profession and the results of his work are in the hands of many famous guitar virtuosos. Whilst this kind of success might seriously inflate many an ego, the way David conducts himself is humility personified.
Given his professional determination as well as the sheer number of hours that are behind his knowledge and success, it’s easy to understand his calmness and confidence in himself as a guitar builder. The longer you talk to him, the more the image of a Zen monk comes to mind.
Time and again David returns to the craft and to the process. The importance of handling the wood correctly, of laying the required cross-section by instinctive feeling, of smoothing the glue in a specific way. Each step is done according to his principles and his process.
Just as violins built by Stradivarius are said to have a soul, so it is that the guitar is a reflection of a part of David's soul.
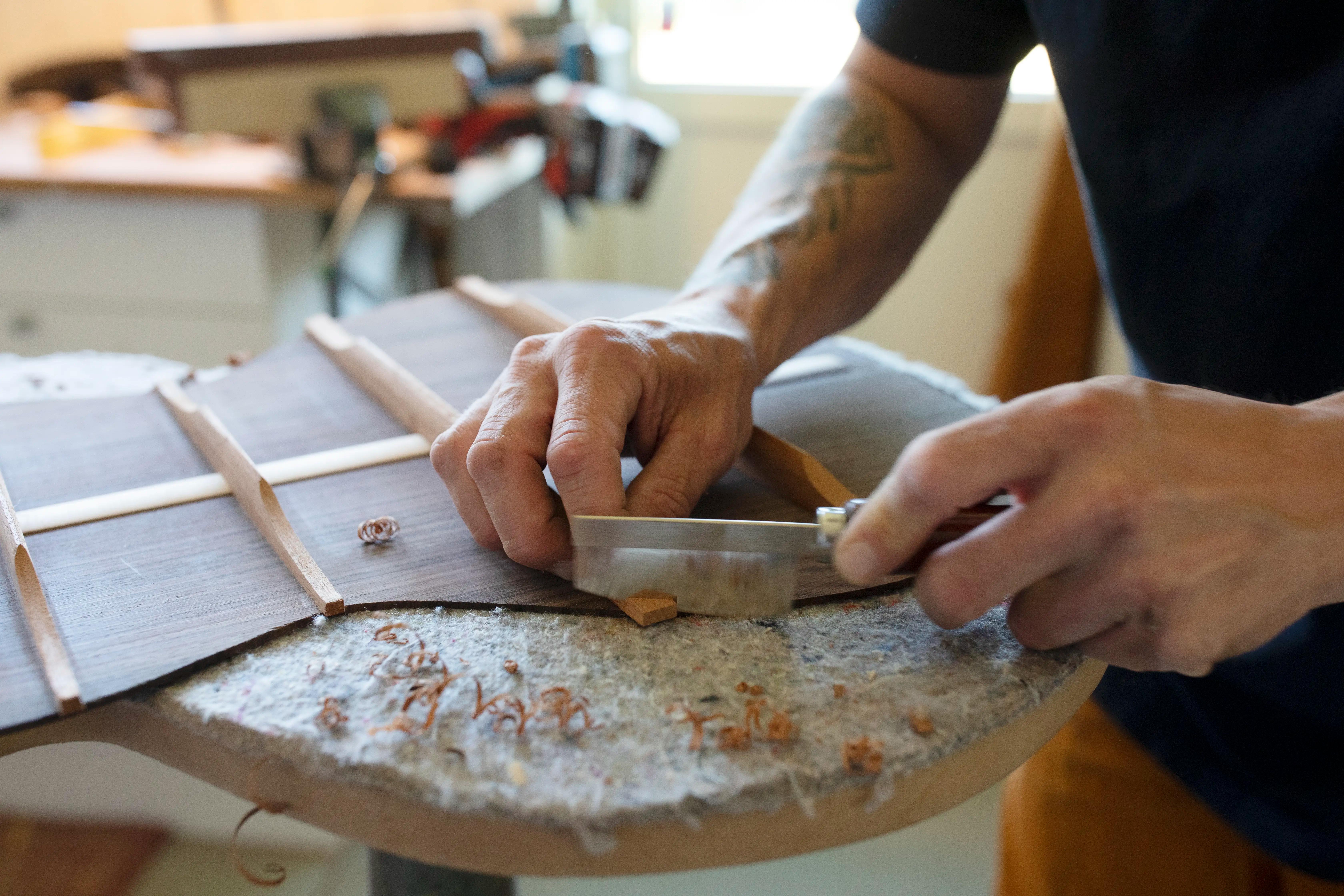
It’s often the case with craftsmen who have extensive knowledge that they don’t feel the need to prove themselves. They are able to quietly listen to what the customer is looking for and if that falls outside the scope of their specialism or expertise they are able to humbly but firmly say no to the request with a simple explanation that “it’s not within the scope of what I do”. This kind of confidence is very apparent in David.
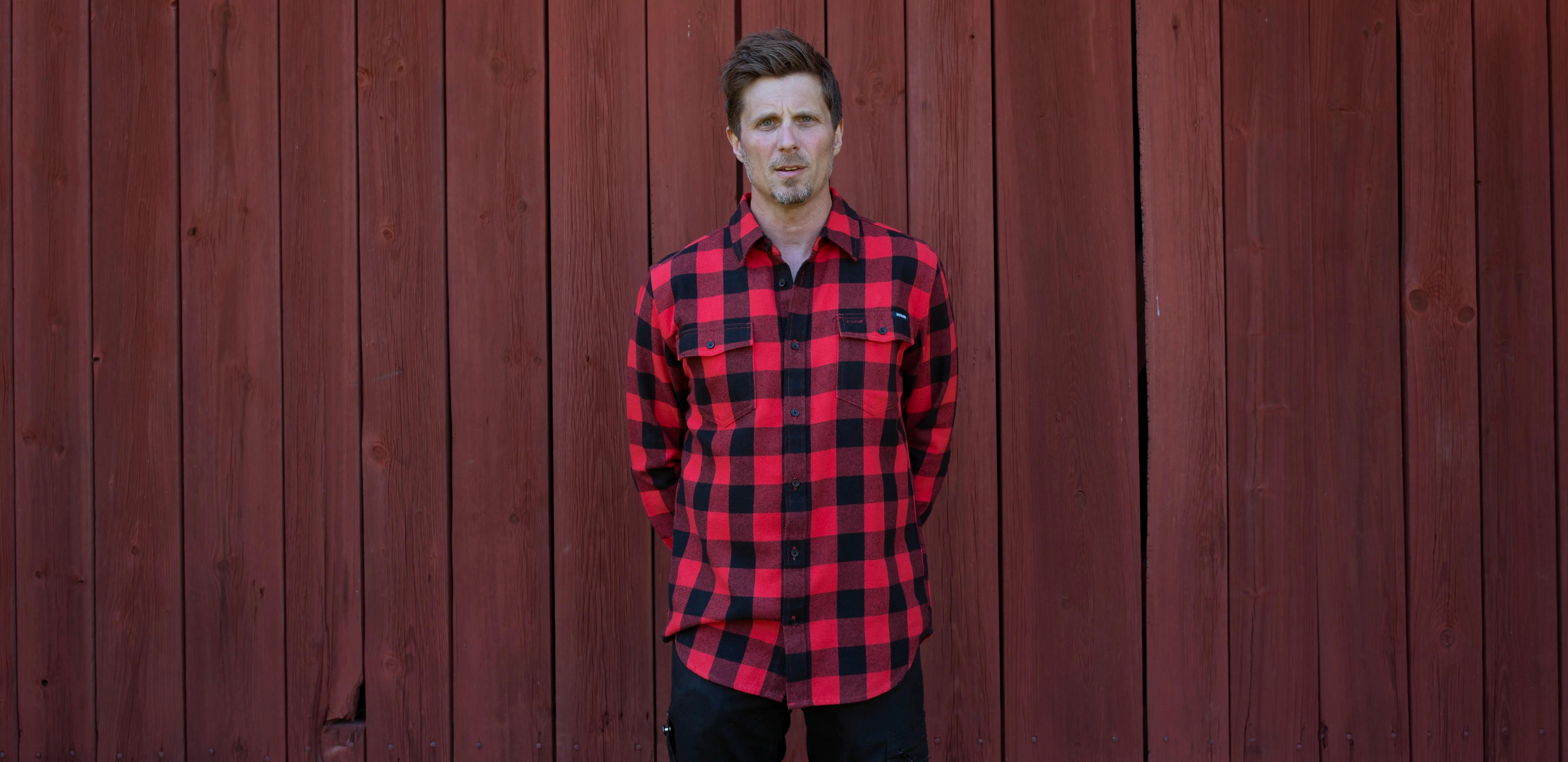
"What ultimately drives and inspires me is when the buyers of my guitars are inspired to write and play beautiful music with the instrument I have built. When this happens, a circle of inspiration is created - I give my all but I also get so much back. That's the best feeling."
During any given working day in David’s workshop he will be working on several different steps involved in the creation of a guitar. Every guitar is built to the specifications of the individual customer and each part plays a decisive role in determining the result: how the guitar should sound.
– My guitars have a specific sound that is basically impossible to copy. This sound is the end product of my unique style and a process that I have refined during the thousands of hours that I have put in right here in the workshop. It is crucial that I achieve the precision of performance that the customer is after.
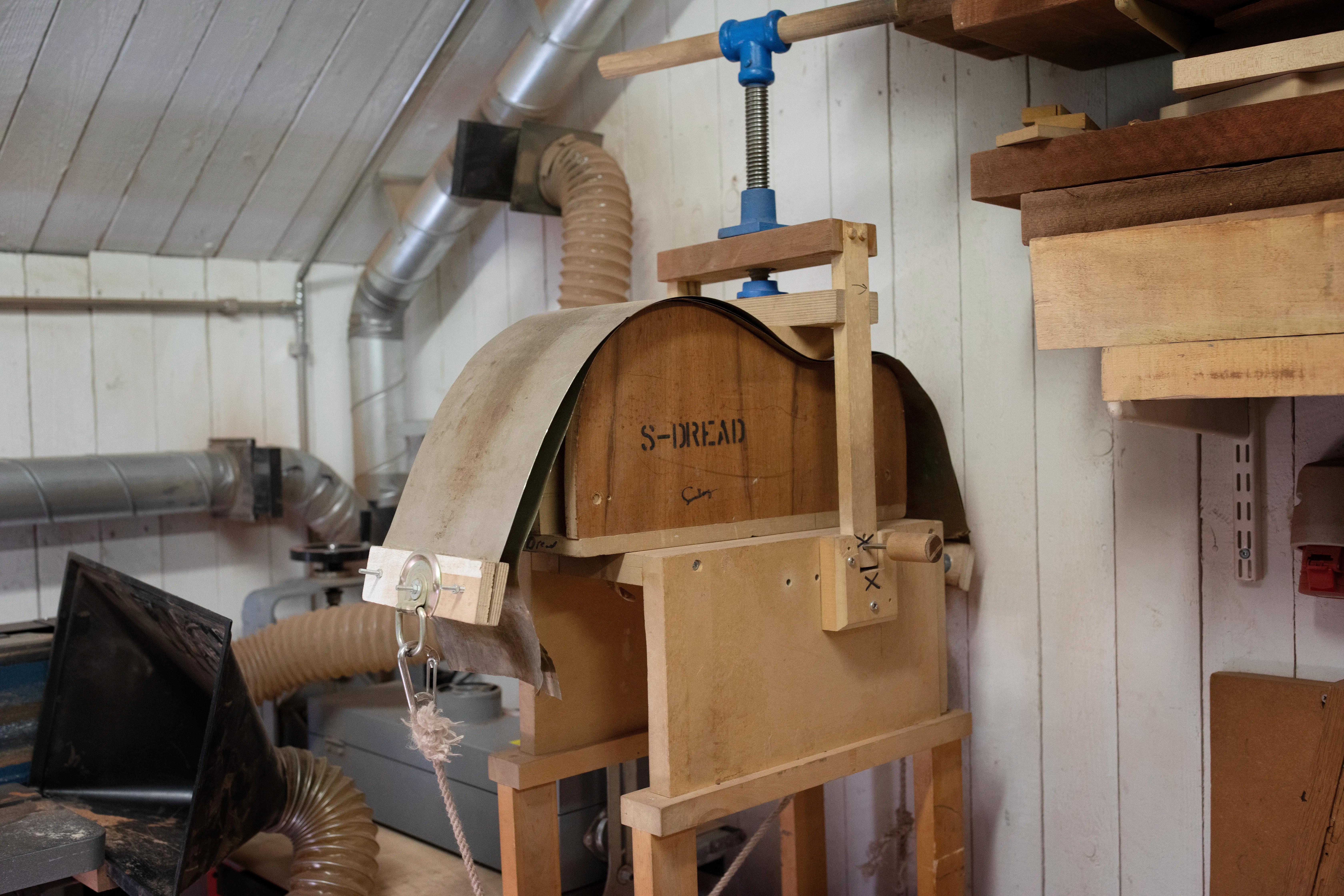
Before David starts building any guitar, he and the customer need to agree on some basic elements, for example the choice of material or the model and size of the basic parts so it will fit the grip of the customer. Once these parameters are determined, it’s left entirely up to David to try to meet, and preferably exceed, the customer's expectations.
– To build guitars as well as it is possible to do, consistently over time, guitar after guitar, it is essential that the wood is treated in a very controlled environment. So the process of building a guitar actually begins long before the customer decides the specifics of what they want.
I cut the wood in specific sizes, plane it to the right thickness and then I spread and stack the wood sheets that I will use the coming years in my workshop. I make sure that a constant temperature and humidity is maintained in this room so the wood stabilises and will keep its shape and performance for many years after the guitar is finished.
This part of the process is fairly basic and relatively simple, but it is super important to make sure that the wood will behave as David want it to once he starts building. It’s just not possible to take shortcuts on something as basic as the wood.
– I would never invest the huge amount of time and effort it takes to build a guitar without trusting that the wood is as well prepared as it can be. It is important to be honest with the customer first and foremost, but also with myself and the guitar.

Different types of wood have different tonal properties. Some types of wood can really be “tone deaf”, regardless of whether they are cheap or expensive. For this reason the choice of wood is the first step in the construction process. You want to choose a type of wood that will “sing” in the way that the customer wants it to. David uses almost exclusively fir, rosewood, mahogany and ebony for his guitars.
It is also important to take care of the guitar and, for example, store it at the right temperature, otherwise there may be problems with cracks or skewing or other issues that might affect the sound.
– The most fun part is the brace shaping, says David. He continues, that's when I decide on the instrument's voice. I am able to determine to a great extent the result of the guitar's sound at that very moment. Sure, all of the steps combined steer the end result in a specific direction (the guitar should function as a unit) but that’s the moment that requires extra focus and concentration. So, if I have a bad day, it's not a good idea to take on this part of the job.
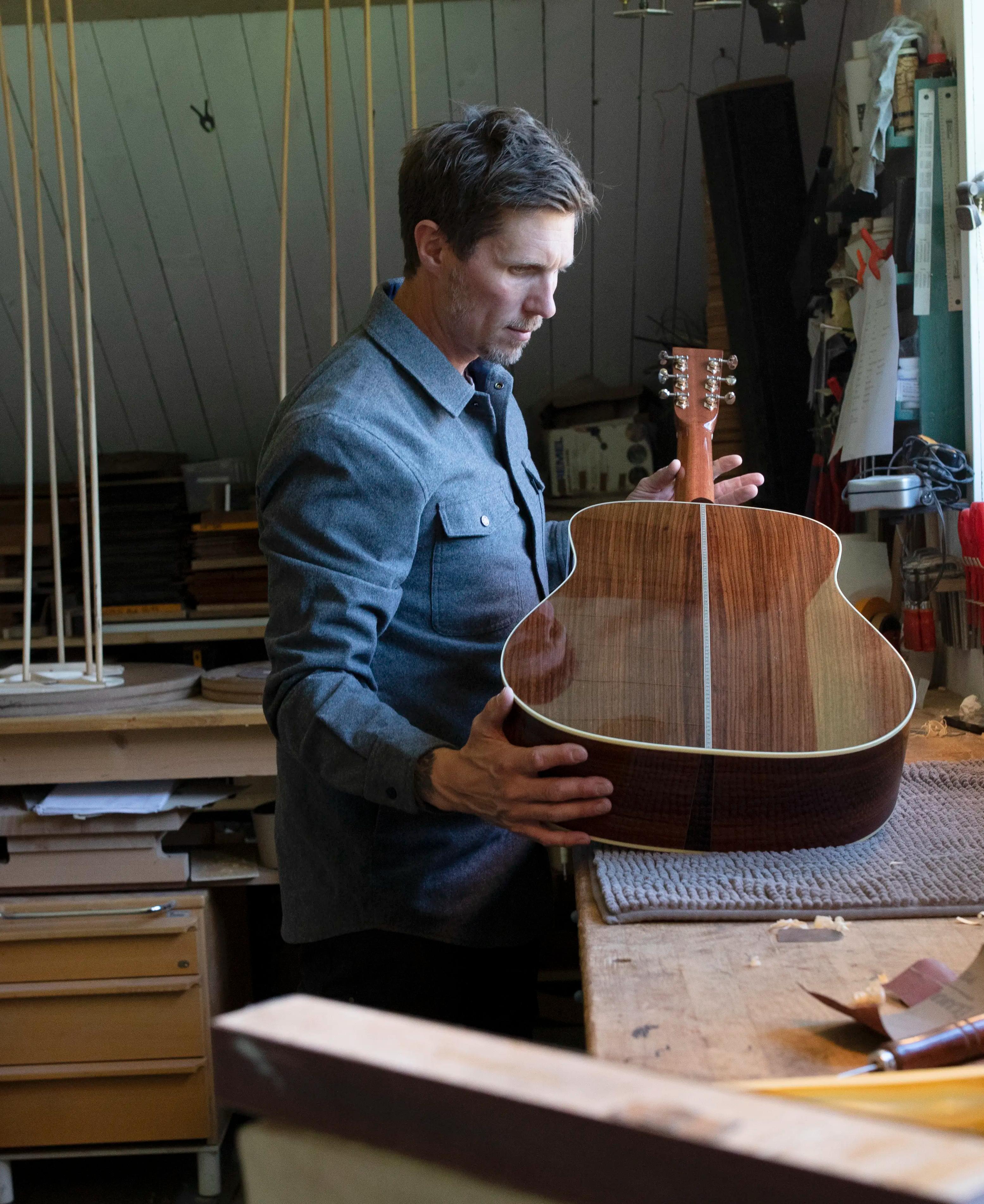
"My guitars have a specific sound that is basically impossible to copy. This sound is the end product of my unique style and a process that I have refined during the thousands of hours that I have put in right here in the workshop."
David lives in the middle of the Swedish countryside, in a red house by the edge of the forest, right next to a winding gravel road. Across the road, a stone's throw from the house stands a barn with a loft that houses his guitar-building workshop.
– It’s a lonely profession but that doesn’t bother me at all. For as long as I can remember, I have always enjoyed being by myself. It’s really only when I meet customers that I spend time with people in my professional life.
I sometimes have interns from the school* that I went to. The teachers have known me for many years and know how I am as a person, so when they have a student who they think would match my profession and personality, they get in touch.
Of course, it’s nice to be able to pass on the heritage of this craft and to sometimes have a work colleague but it also reminds me why I have chosen to work alone.
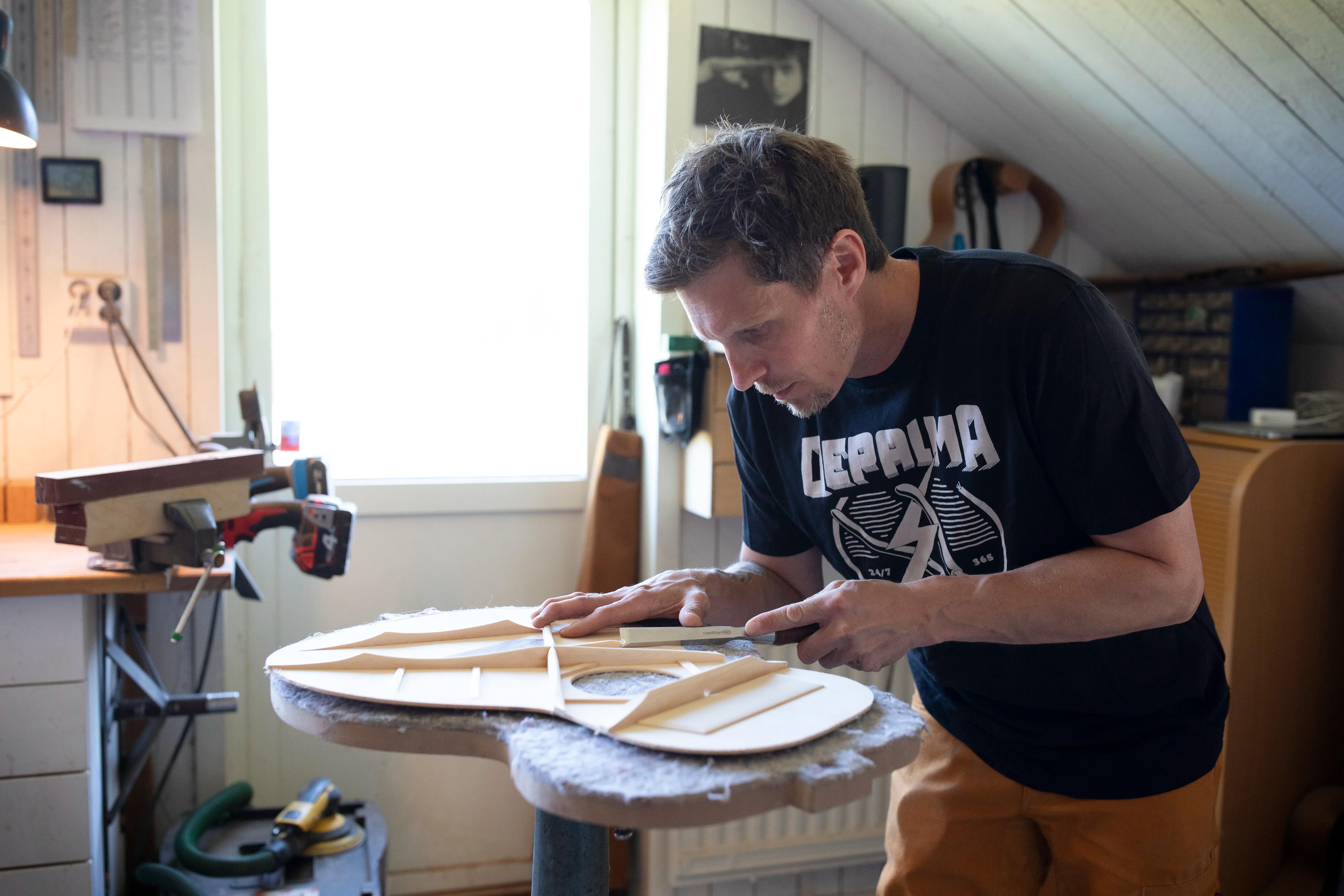
With the skills of craftsmanship that David possesses, it’s easy to presume that he would try his hand at building other products but this couldn’t be further from the truth.
– I have the skills and experience to be able to create many other things with wood, like furniture or whatever it may be - but it doesn’t appeal to me at all.
What ultimately drives and inspires me is when the buyers of my guitars are inspired to write and play beautiful music with the instruments I have built. When this happens, a circle of inspiration is created - I give my all but I also get so much back. That's the best feeling.
Hard facts
David's workshop is certainly not a big space but it seems to be perfectly adapted to his needs. The tools hang perfectly in their places and the drawers are organised chaos full of Japanese and Canadian chisels, planers and mini planers, scrapersand rulers.
Through thousands of hours of crafting, some tools have become firm favourites over the years, so much so that they are almost an extension of himself, an inextricable part of his creative instinct.
Find David on Instagram and visit sundbergguitars.com.
David's Outfit
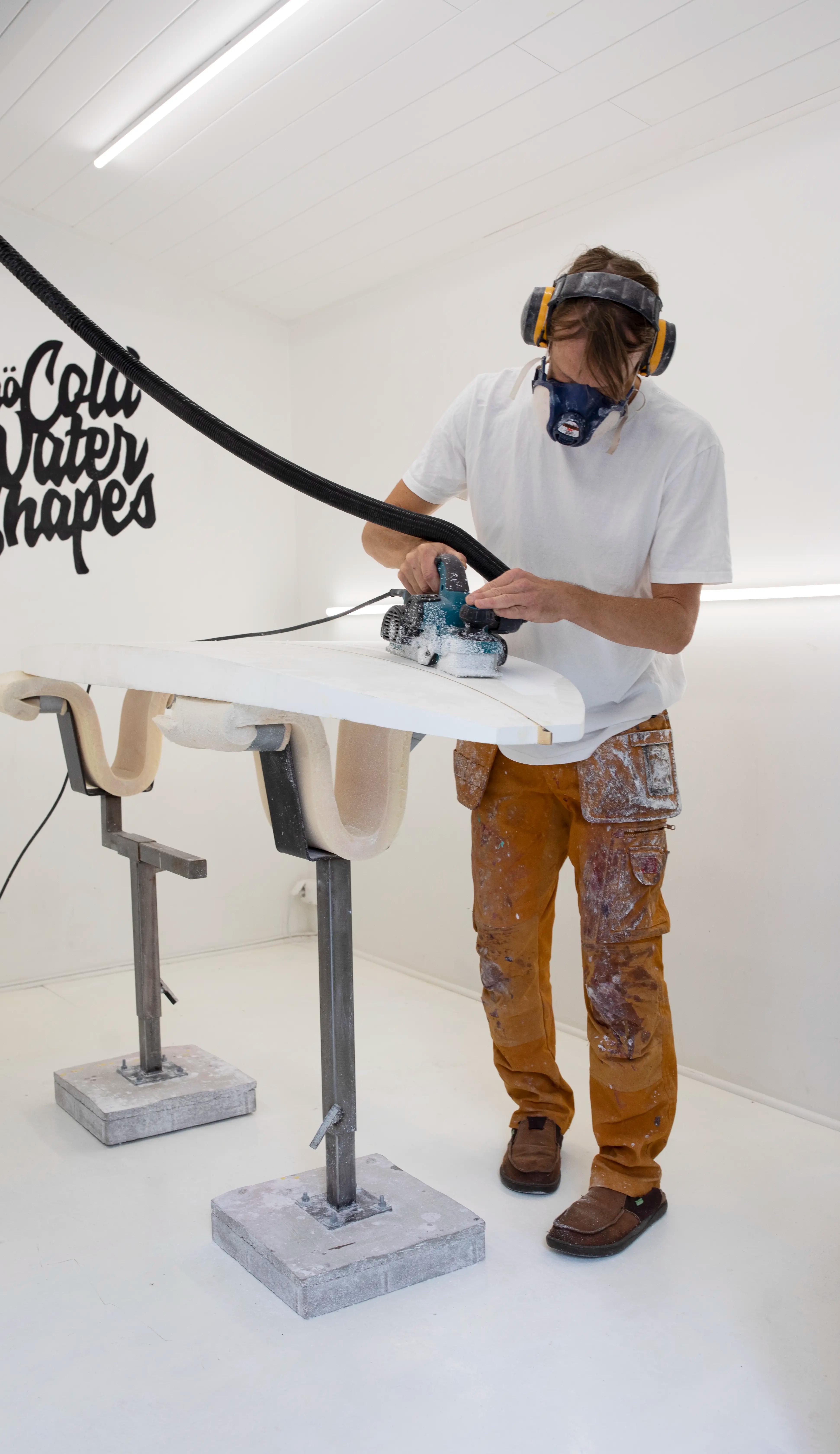
Craftsmen Stories
Mattias - Surfboard Shaper
Surfboard shaper with his own shack a stone's throw from Sweden's surf mecca on Torö Stenstrand.
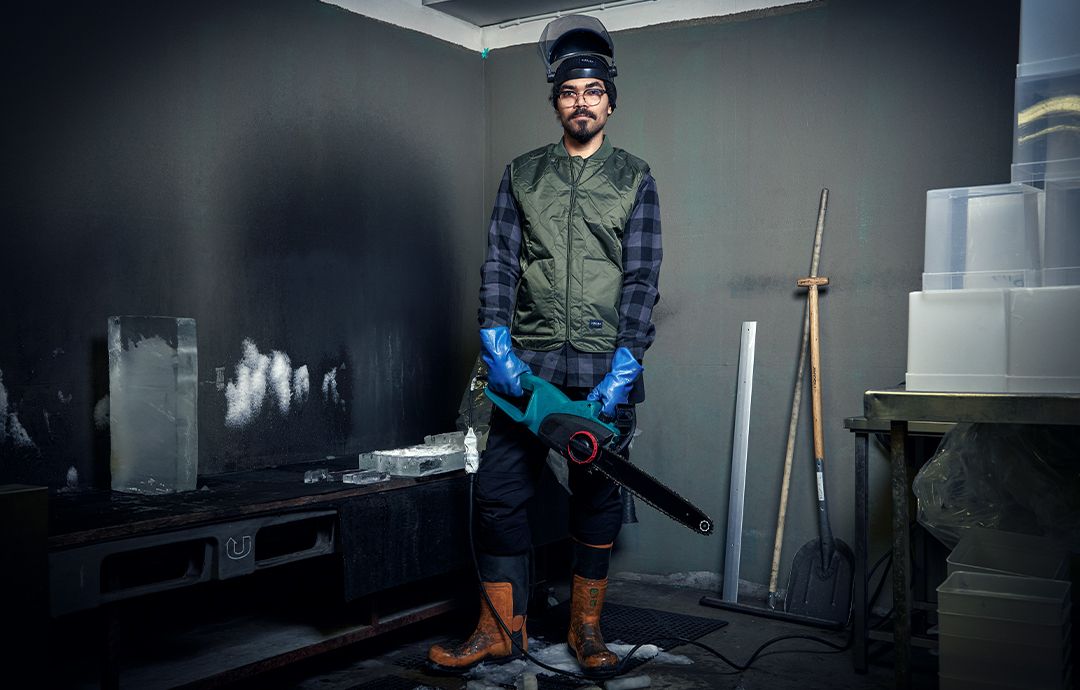
Craftsmen Stories
Johan - Ice Cutter
After more than six years working as an Ice Cutter, Johan is an expert in producing and cutting crystal clear ice, that gets served in drinks at some of the finest restaurants and bars.